Quick Answer
Product development costs for a new product vary greatly depending on complexity, certifications needed, and manufacturing. Typically, a new product costs between $20,000 and over $1 million to develop.
Launching a new product is exciting, but it’s important to flesh out some important details during the planning process, including product development costs. Without a rough estimate, it’s difficult to budget, secure funding from investors, and get a solid return on your investment.
In this post, you’ll learn 10 product development costs to consider, like the various types of engineering, and how to develop a proper estimate. With this information, you can plan your next product design properly by minimizing surprise costs that can derail your project.
How Much Does It Cost To Develop a Product?
Development costs for a new product can range anywhere from $20,000 to $30,000 on the lower end to well over $1 million on the high end. There are many different variables to take into consideration when creating a new product. For example, industrial engineering alone can range from $15,000 to $60,000, and medical device certifications can cost upwards of $100,000.
Additional key factors that influence product development costs include research and development, prototyping, manufacturing, and shipping. Knowing what costs are involved with your upcoming product and using tools like a product requirements document (PRD) can assist you with an estimate before you begin the work.
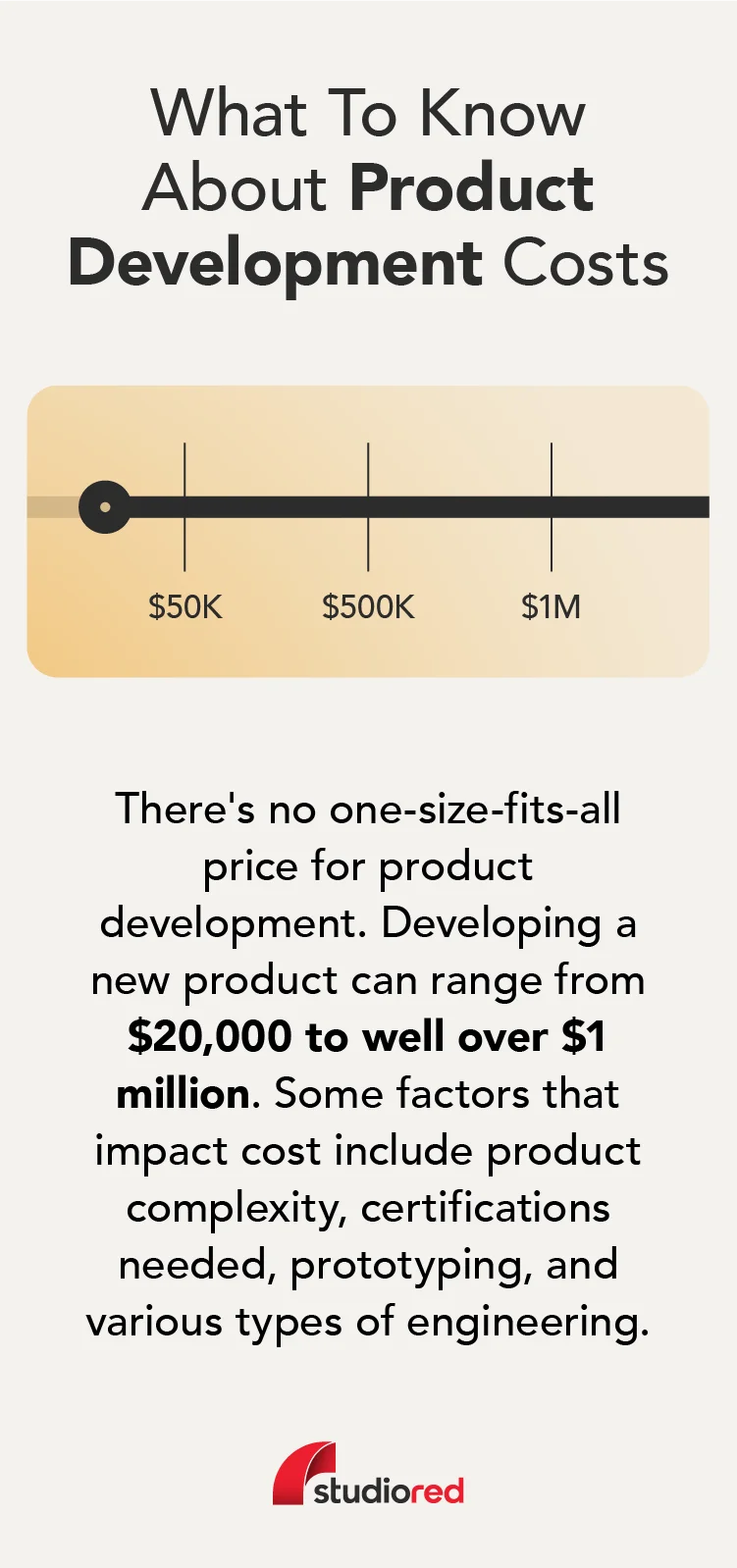
10 Must-Know Product Development Costs
Developing a new product can involve a significant investment, and the costs should be a prime consideration for any business throughout the development cycle. In this section, we go over 10 factors that can affect the cost of your product, and some insight into what each one entails.
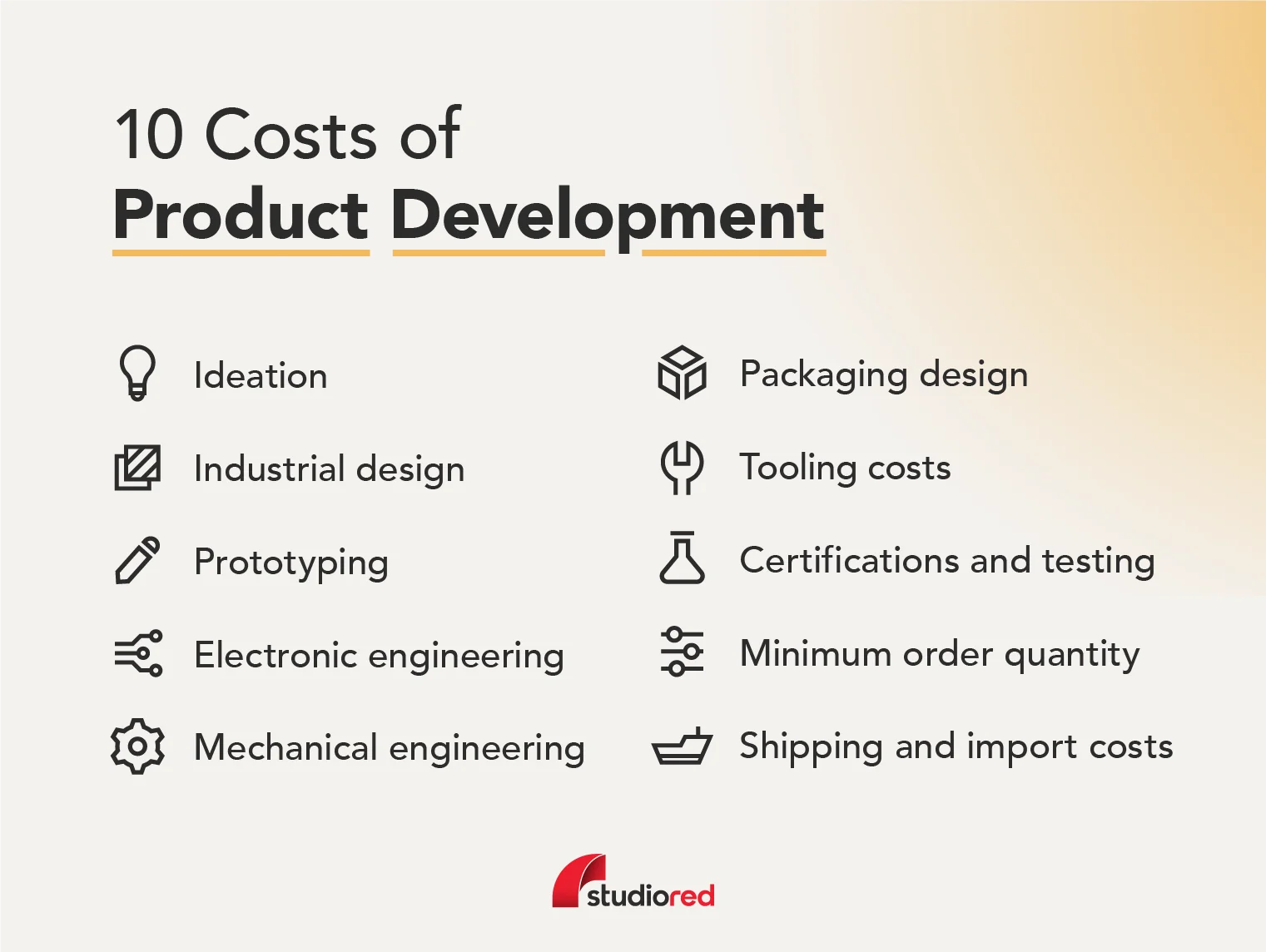
1. Ideation
Average cost: $10,000-$35,000
Ideation is the first step of the design process, and it includes the bulk of the work when hiring an outside company. During this phase of development, a product design company spends a lot of time making plans to turn your vision into reality. The ideation phase can include brainstorming sessions, user research, and market analysis, ensuring your product achieves your business’s overarching goals.
Should your company decide to do the ideation process internally, it could cost $10,000 or less.
2. Industrial Design
Average cost: $15,000-$60,000
The cost of development for industrial design includes the time and equipment designers need to address everything from human factors design to creating models. Designers are concerned with how users will interact with the product while ensuring the product does what it’s designed to do. This also involves creating 3D models that are later used to create prototypes and the final product.
3. Prototyping
Average cost: $5,000+ per iteration
Prototype costs can vary, though they’re typically a minimum of $5,000 per iteration, and some complex prototypes can cost upwards of $250,000. The parts and materials used for the prototypes can increase the cost, and each version of the prototype has a cost as well. Prototypes can range from low- to high-fidelity, and depending on the product, these may need different materials that range in cost.
4. Electronic Engineering
Average cost: $20,000+
If your product involves electronic components, it will need electrical engineers as well as the necessary parts. The parts can include physical parts like wires and circuit boards or the time and parts needed to create software and firmware. For example, there are additional costs if your product is designed to connect to a mobile app or a wireless network.
5. Mechanical Engineering
Average cost: $30,000-$100,000
Mechanical engineers are responsible for making sure products are functional, safe, and efficient. The mechanical engineering phase can include creating 3D models, conducting stress and vibration analysis, and selecting the proper materials. Engineers may also be involved in overseeing the manufacturing process.
While the higher end of mechanical engineering can reach $100,000, the price can increase beyond that for more complex products that involve robotics.
6. Packaging Design
Average cost: $0-$20,000
Whether you’re creating a commercial product for everyday people or a product for businesses, it needs good packaging. The packaging tells a story about the product and your brand, and it directly impacts how the product sells. This phase includes the time needed for a graphic design team to design the package and materials and production of the packaging. In some cases, the packaging manufacturer will create very basic packaging at no cost.
7. Tooling Costs and Manufacturing Setup
Average cost: $10,000-$50,000
Mass production is one of the highest product development costs. The product design company you work with needs to create molds for each part, also known as “tooling” in manufacturing. The price range largely depends on the count, sizes, and complexity. For more involved products, tooling costs can run well over $1 million.
8. Certifications and Testing
Average cost: $5,000-$2,000; $100,000 for medical devices
Before going to market, products must be tested and meet different regulations. In the United States, your product may need an FCC certification for electrical products, and there are different certifications in the EU. Medical devices require more expensive certifications, like 510(k) clearance with the FDA or premarket approval (PMA). The product will need to pass various tests to meet the certification standards.
Some common certifications include:
- FCC certification (United States)
- UL certification or CSA certification (United States and Canada)
- CE certification (European Union)
- RoHS certification (European Union and California)
9. Minimum Order Quantity (MOQ)
Average cost: $25,000+
Once you’re ready to create the final product, you’ll have a minimum order quantity for your first batch. Typically, you’ll need a minimum of 100 units, and the development costs increase as the quantity increases. Each unit has parts that must be manufactured as well.
When shopping around for manufacturers, it may be tempting to get the best price, but it’s also important to make sure they’re providing you with a final product that meets your standards.
10. Shipping and Import Costs
Average cost: $5,000+
The price range of shipping costs for a new product can vary drastically. Order size and weight are major factors and can also depend on where your manufacturer is located. For example, if your manufacturer is in China and you’re shipping to the United States or other countries, you’ll generally pay less than if your manufacturer is located in Europe, though it depends on transportation type, customs duties, and import taxes.
How To Estimate Product Development Costs
Accurately estimating product development costs requires a structured approach. By breaking down the development process into distinct stages with a PRD template, businesses gain a clearer picture of the associated expenses at each phase.
Design and Engineering
This initial stage focuses on translating your ideas into a functional product blueprint. Here, the costs you’ll incur are associated with a team of product designers and engineers creating designs, specifications, and prototypes.
Questions to ask:
- How complex is this product? Take a look at your product and think about how simple or complex it will be. When you start including electronics and different mechanisms, the cost will likely increase.
- How many iterations do we expect to have for our prototypes? You may need to create different versions of the prototype to test out different aspects like ergonomics. It’s safe to assume you’ll need at least three to five iterations for your project, but it could be more for more complex products.
- What materials are required for this product? Think about what types of materials your product will require and if there are reliable, more affordable alternatives to any parts.
- What types of prototypes will we be using, and will they be high- or low-fidelity? Digital and physical prototypes will have different costs. Some products, like those that include software, will need both physical and digital prototypes.
Production
When it’s time to turn your finalized design into a physical product for launch, there are costs associated with manufacturing your product in bulk.
Questions to ask:
- How much are the tooling costs? Tooling costs can vary greatly depending on the complexity of the parts, as well as part count.
- What manufacturing methods will we use? Think about your budget and the process of vetting different manufacturers.
- What’s the MOQ? Consider how many units you want for your first run. The order quantity directly affects the initial production costs.
- How long will it take to manufacture a batch of our product? Longer product lead times may require you to order a larger volume for your batches.
Distribution
Once the product is manufactured, distribution involves getting your product from the factory to your customers. These costs include warehousing, shipping, and fulfillment. This may also involve working with retailers and other third parties like wholesalers or third-party logistics (3PL) providers.
Questions to ask:
- What distribution channels will we use? The product may be sold directly, through retail locations, or online marketplaces. Each distribution method may have different costs, and don’t forget to consider marketing and post-production costs as well.
- Where is our target market located? Where your product is warehoused and where your customers are located can introduce additional shipping and distribution costs. For example, rural areas may cost more to ship to due to longer delivery routes and low population density.
- What are the warehousing costs? Your product inventory will need to be stored somewhere, and if it’s at a different location than your place of operations, it will have a separate cost.
- What’s our return policy? Ideally, every customer will be satisfied, but you may encounter return requests. Return shipping costs can impact profitability unless the cost is passed on to the customer.
Tips for Reducing Product Development Costs
Controlling costs is critical for the success of any product development project. In this section, we explore some practical strategies and best practices for minimizing expenses while maximizing value.
Research Vendors
Thorough vendor research allows you to compare costs, but this doesn’t mean you should always choose the cheapest vendor. Consider a few different criteria when vetting vendors, like cost, experience, and willingness to negotiate favorable terms. Choosing a manufacturer with expertise in your specific product area can also help optimize your budget and potentially reduce product costs.
Be Efficient With Resources
Being mindful of resource allocation throughout the product lifecycle can directly translate to cost savings. Creating streamlined workflows and focusing on product management helps reduce wasted time and effort. To maximize efficiency, assign tasks to people with the right skill sets to avoid quality issues and delays.
It’s also helpful to hold regular team meetings to discuss the progress of different teams. During these meetings, identify current and potential roadblocks and try to brainstorm solutions. This collaborative approach fosters open communication and allows for proactive problem-solving.
Keep Manufacturing Top of Mind
While the initial design phases focus heavily on functionality and aesthetics, keeping an eye on manufacturability from the outset can significantly reduce costs down the line. Throughout the design process, think about parts, materials, tooling, and how they’ll impact the cost of manufacturing.
Being cognizant of part complexity can reduce manufacturing costs. Products with fewer parts are generally cheaper to manufacture. For example, you may be able to achieve the goal of your product with a single, multi-purpose part rather than using multiple, smaller components.
Choose the Right Product Development Company
The right product development company has expertise in your specific type of product and is willing to work with you based on your budget and project scope. Experienced product development companies can also use their expertise to help you find areas where you can reduce development time and costs.
Just like finding the right manufacturer, research product development companies. Review their portfolio to see if they’ve created products similar to yours. Their website most likely has a client roster showcasing brands they’ve worked with in the past.
Get the Most Out of Your Product Development Budget With StudioRed
Developing a new product is a significant investment, but working with an experienced product development company can save you money while also helping you create the best possible product. At StudioRed, we understand the importance of managing costs while bringing your vision to life. Our team of designers and engineers is here to help you from concept to commercialization.
We’re here to ensure your project stays on track and within budget. We also offer a wide range of services, specializing in industrial design, mechanical engineering, prototyping, and much more. Get in touch today for a consultation and to learn more about how we can help with your next product.