Quick Answer
Prototype manufacturing is the process of creating one or more early test versions of a new product design to evaluate and refine key aspects like form, fit, function, manufacturability, and market viability before committing to mass production.
What Is Prototype Manufacturing?
Prototype manufacturing is the process of creating a preliminary three-dimensional model or early sample of a product before manufacturing the final version, like 3D product rendering for example. It allows designers to evaluate the feasibility, functionality, and performance of their concepts before investing in full-scale production.
Think of a prototype like a “test run” that allows inventors and product developers to identify and fix problems early on when changes are easier and less expensive to implement. You should plan to build and develop a prototype after creating your initial design for a product but before manufacturing engineering and mass production.
You can fabricate different types of prototypes in a number of ways depending on the nature of the product and the tools you have available. The most common processes include:
- 3D modeling: This is the process of creating a digital rendering of a physical product using computer-aided design (CAD) software. It allows for design optimization, visualization, and refining before physical production.
- 3D printing: This is an additive manufacturing process that builds objects layer by layer using materials such as plastic, resin, or metal. It’s best for rapid prototyping, complex geometries, and low-volume production.
- CNC machining: Also known as computer numerical control, this subtractive manufacturing process uses automated tools to remove material from a solid block or sheet. It’s great for creating high-precision parts like gears or enclosures, working with a variety of materials, and medium-volume production.
- Injection molding: This process involves inserting molten material (usually plastic) into a mold cavity, which then hardens to form the intended shape. Injection molding is a versatile technique used for producing a wide range of plastic products, from everyday toys to complex medical implants, thanks to its ability to deliver consistent, accurate parts at high volumes.
- Handcrafting: This traditional manufacturing method involves creating prototypes or products by hand using manual tools. Handcrafting offers high flexibility and customization but is labor-intensive and not suitable for large-scale production.
The method you choose depends on factors like design complexity, material requirements, necessary tolerances, production volume, and budget constraints.
The prototyping process is rarely linear. It often requires multiple iterative cycles of building, testing, evaluating, and refining designs based on real-world performance, user feedback, and lessons learned about manufacturability. The end goal of prototype manufacturing is to finalize an optimal design that meets customer needs while considering the practicality of manufacturing at scale.
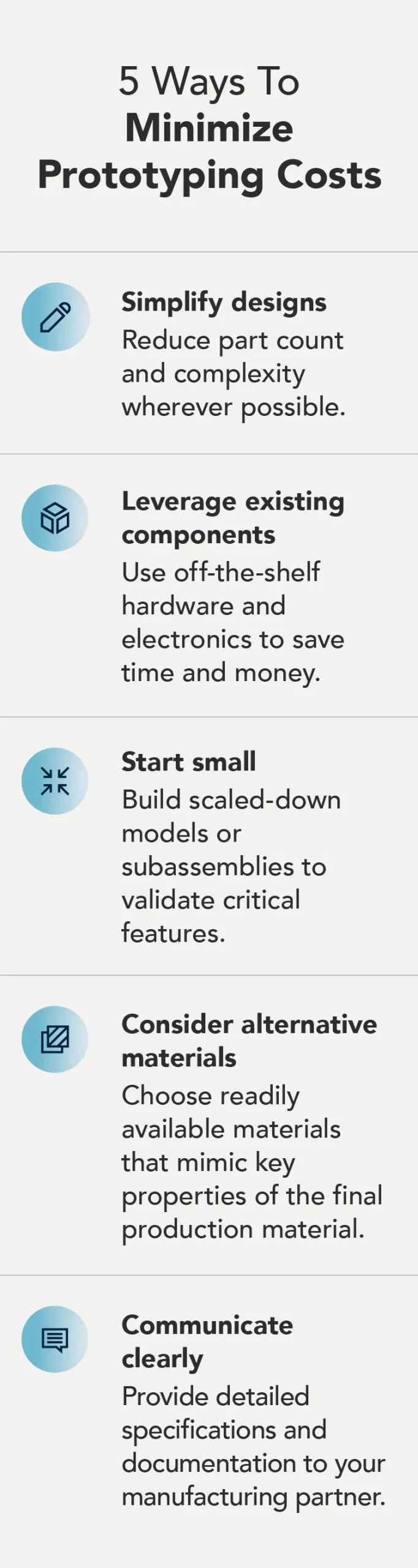
Importance of Prototypes in Product Development
Prototype manufacturing plays a pivotal role in de-risking, improving, and accelerating the product development process. Specifically, prototyping helps you:
- Test and refine product designs: Testing allows you to identify and address design flaws or usability issues before investing in mass production. Based on testing and feedback, you can iterate on your design and continuously improve it.
- Evaluate manufacturing processes: Prototype manufacturing helps you uncover any potential production challenges, such as part fit or assembly problems, that may arise during the actual manufacturing process. This allows you to address these issues early on.
- Verify product functionality, usability, and market appeal: Prototyping allows you to test how the product works, how easy it is to use, and whether it solves a genuine problem for your target customers. Before launching a product, gather feedback from potential customers. Their input can validate that you’re headed in the right direction or signal needed changes to the design or target market.
- Showcase ideas to secure investments: Potential investors are more likely to provide funding for a product idea if they can see and interact with a tangible working prototype rather than just a business plan.
The Prototype Manufacturing Process
There are several key steps you need to follow when creating a prototype. Let’s dive into each stage of the process:
1. Conceptualization and Design
Every prototype begins with brainstorming sessions to explore concepts and possibilities. This is where team members hash out the general vision and functionality of what you want to build.
Once you have a solid concept, flesh out all the details of your design, including measurements, materials, features, and anything else that defines your product. You can use these specifications to estimate costs and guide the manufacturing process.
Sketches and 3D modeling are useful for determining the overall shape and dimensions of a prototype. However, CAD designs don’t always account for real-world engineering challenges. This is why it’s important to keep pragmatic concerns in mind during this creative phase. Consider how all the separate components will fit together in the final physical prototype. Some parts may need to be simplified or removed to make production feasible.
2. Material Selection
When choosing materials for your prototype, you’ll want to consider several factors. Cost and availability are usually high on the list. More affordable and readily available options like wood, plastic, and metal alloys are popular for prototypes.
The materials you choose also depend on how durable you need the prototype to be. If it’s an early concept model, wood, foam, or 3D-printed plastic might work well. For a working prototype exposed to real-world conditions, you’ll want something more rugged, like aluminum or steel alloys.
Material | Key Properties | Typical Uses | Ideal Prototyping Techniques |
---|---|---|---|
Acrylonitrile Butadiene Styrene (ABS) | Strong, heat-resistant, impact-resistant | Functional prototypes, durable enclosures, snap-fit parts | FDM 3D printing, CNC machining, injection molding |
Polylactic Acid (PLA) | Biodegradable, easy to print, low warping | Concept models, visual prototypes | FDM 3D printing |
Polycarbonate | High strength, transparency, heat-resistant | Enclosures, optical parts, durable prototypes | FDM 3D printing, CNC machining, injection molding |
Acrylic (PMMA) | Transparent, rigid, good weatherability | Displays, visual prototypes, light guides | Laser cutting, CNC machining |
Resins | Range of properties (hard, flexible, heat-resistant) | Detailed models, molds, functional parts | SLA/DLP 3D printing, casting |
Foam | Lightweight, easily shaped | Concept models, packaging mockups | Hand carving, hot-wire cutting, CNC machining |
Paperboard & Cardboard | Inexpensive, easy to work with | Early concept models, packaging mockups | Cutting, folding, gluing |
Medium-density fiberboard (MDF) | Smooth surface, dimensionally stable | Jigs, fixtures, models for painting/finishing | CNC machining |
Aluminum | Strong, lightweight, good machinability | Functional prototypes, metal-like appearance | CNC machining, sheet metal fabrication |
Steel | Very strong, durable | Heavy-duty prototypes, testing structural integrity | CNC machining, welding |
Wood | Natural aesthetic, varying strength and density | Concept models, furniture prototypes, visual mockups | CNC machining, woodworking techniques (cutting, joining) |
Composites (e.g., carbon fiber, fiberglass) | Exceptional strength-to-weight ratio, stiff | High-performance parts, structural prototypes | Layup techniques, CNC machining, 3D printing |
3. Rapid Prototyping
Rapid prototyping is a set of techniques for quickly fabricating a scale model of a physical part or assembly using 3D CAD data. Some common rapid prototyping technologies include:
- Stereolithography (SLA) uses an ultraviolet laser to cure liquid resin into plastic parts.
- Selective laser sintering (SLS) uses a laser to melt powdered materials like nylon into solid parts.
- Fused deposition modeling (FDM) extrudes molten plastic materials to form layers.
The main benefits of rapid prototyping are speed, low cost, and complexity. Parts can be ready in hours instead of weeks, and you can churn out dozens of prototypes for the same price you would pay for one machined part. Plus, it lets you create complex geometries that would be tricky to achieve with traditional machining.
However, rapid prototypes have some limitations. They tend to be less durable and dimensionally accurate than machined prototypes. The materials are often limited to plastics, resins, and powdered metals. Also, rapid prototyping may require additional finishing work to improve the surface finish.
For many product developers, the speed and low cost of rapid prototyping outweigh these limitations. It allows for accelerated design iteration and testing before investing in tooling for production parts.
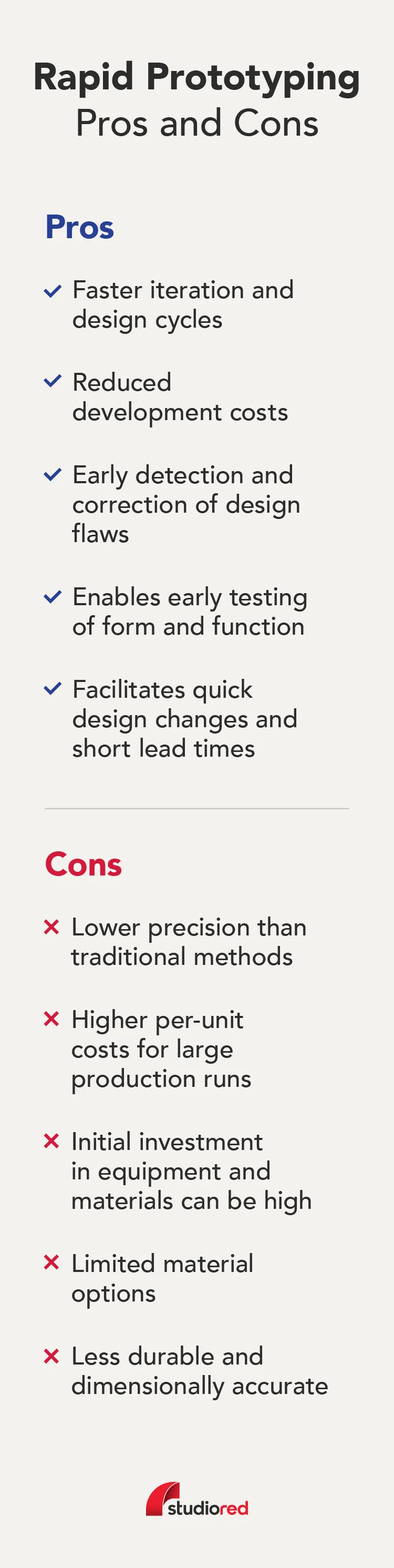
4. Assembly and Integration
Once the individual components of the prototype have been manufactured, the next step is to assemble them into a complete, functional unit. This process involves carefully fitting and securing the parts together, ensuring proper alignment, and testing for any interference or compatibility issues.
First, determine how the electronic, mechanical, and structural elements will be integrated. Map out the assembly sequence, identifying any interdependencies and utilizing geometric dimensioning and tolerancing (GD&T) principles to ensure proper fit and functions. For example, certain wires or components may need to be installed before the enclosure is sealed shut, and GD&T can help ensure these components are properly aligned and secured. Solve any potential challenges on paper before physical assembly begins.
During assembly, double-check that each piece is oriented and installed correctly. Even small mistakes can impact functionality and require disassembly to fix, costing time and money. When possible, test individual modules before integrating them into the larger prototype. This helps isolate any issues and makes troubleshooting easier.
To overcome challenges, it’s important to have a well-organized assembly plan, clear documentation, and skilled technicians who can identify and resolve issues quickly.
5. Testing, Iteration, and Refinement
Once you have a working prototype, it’s time to put it through rigorous testing. Various tests help identify issues before ramping up to full-scale production. Common types of tests include:
- Functional testing verifies that the prototype performs its intended functions correctly and reliably.
- Durability testing assesses the prototype’s ability to withstand normal wear and tear, as well as extreme conditions such as impact, vibration, and temperature fluctuations.
- Usability testing gathers feedback from potential users to evaluate the prototype’s ease of use, ergonomics, and overall user experience.
Based on the results of these tests, designers can identify areas for improvement and modify the prototype as needed. This iterative process of testing, refining, and retesting is crucial for optimizing the prototype’s performance and ensuring a successful final product.
By the end of this stage, you will likely have gone through several iterations before achieving the perfect prototype. But reaching this milestone means you now have a production-ready representation of the final product to show investors, buyers, and users.
Considerations in Prototype Manufacturing
When approaching prototype manufacturing, there’s a lot to think about to ensure your prototype effectively serves its intended purpose and helps bring your product to market faster and more cost-effectively.
Purpose and Fidelity
The primary goal of your prototype determines the type you need. What questions are you trying to answer? What hypotheses are you testing? Common purposes for prototypes include:
- Proof of concept (POC) prototypes: These are very basic, often non-functional models used to demonstrate the feasibility of an idea or core functionality. POC prototypes are usually built quickly and inexpensively using readily available materials.
- Visual prototypes: Also known as looks-like prototypes or appearance models, visual prototypes accurately represent the shape, size, color, and finish of the intended final product. They are non-functional and are used for market research, gauging customer reactions, and pre-sales.
- Functional prototypes: These works-like models closely resemble the final product in both form and function. Functional prototypes are used for extensive testing and refinement to ensure the product performs as intended under real-world conditions.
- Pre-production prototypes: Often called pilot runs, zero series, or looks-like/works-like prototypes, these are essentially final products made using the intended mass-production processes and materials. Pre-production prototypes serve to validate the manufacturing setup and identify any remaining issues before committing to full-scale production.
The purpose of your prototype will dictate the level of fidelity required. Fidelity refers to how closely the prototype matches the final product in terms of appearance, functionality, and material properties. Fidelity ranges from low (rough, quickly made models) to high (near-perfect representations of the end product).
High-fidelity prototypes, like pre-production prototypes, deliver the most realistic results but also require more time and money to develop. Low-fidelity models, like POC prototypes, are faster and cheaper to produce but may not fully answer all your design questions.
By carefully considering the purpose and required fidelity of your prototype upfront, you can make smart decisions about materials and manufacturing methods downstream.
Manufacturing Methods and Materials
When choosing a prototype material, consider both your fidelity requirements and the properties of the final production material. Do you need an exact match in terms of strength, flexibility, thermal stability, chemical resistance, or other characteristics? Or is visual similarity more important for this prototype?
Certain manufacturing methods and materials may be more readily available, affordable, and suitable for your specific prototype requirements. For example, 3D printing with thermoplastics can be a cost-effective way to produce low-fidelity prototypes, while CNC machining or injection molding may be better suited for higher-fidelity, functional prototypes.
Budget and Timeline
Budget and timeline are key drivers in any prototype manufacturing project. The level of complexity, material selection, manufacturing method, and required quantities all impact the bottom line. It’s important to have a clear understanding of these factors upfront to avoid unpleasant surprises down the road.
Rapid prototyping techniques like 3D printing can churn out a basic prototype in a matter of days, while more intricate designs requiring custom parts and tooling will take much longer. If speed is a priority, opt for a scaled-down model focusing on key features rather than a fully functioning prototype.
Using off-the-shelf components where possible, onshoring manufacturing, and simplifying the design can help reduce costs. For example, a POC prototype demonstrating key product features may not require the level of polish and precision needed for a production-ready model.
Work closely with your prototype manufacturing partner to set realistic expectations around lead times and deliverables. Give them as much information as possible about your schedule constraints and upcoming milestones. Be prepared to make trade-offs between speed, cost, and quality to meet your deadlines.
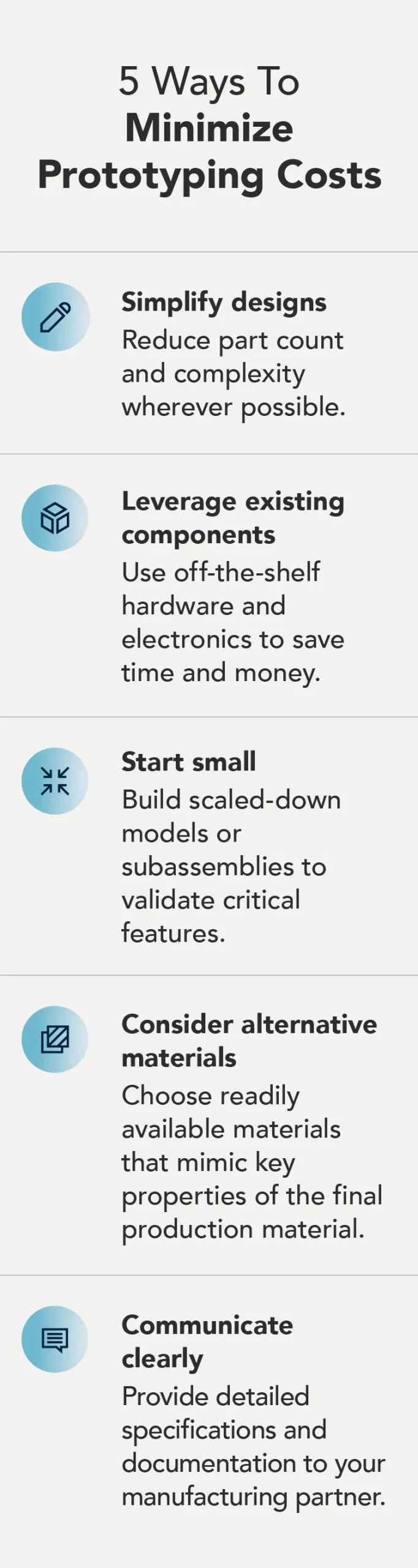
Intellectual Property Considerations
Protecting your intellectual property (IP) should be a top priority in any product development effort, including prototype manufacturing, to protect your ideas and designs from theft or unauthorized use by others.
- Patent protection: Before working with any external prototype manufacturing partners, consider filing a provisional or utility patent application to establish a “priority date” for your invention. While patents can be expensive and time-consuming to obtain, they may be worth it for truly novel products or technologies.
- Non-disclosure agreements (NDAs): Use NDAs when sharing sensitive information with prototyping vendors and suppliers.
- Restricted access: Limit access to essential key files, data, and documentation to only those individuals who absolutely need it.
- Control information sharing: Be judicious about what you share, especially in the early stages of prototyping. Don’t disclose any more than is necessary for the manufacturer to do its job. To limit exposure, consider breaking your design into subassemblies that can be produced by different vendors.
- International considerations: If you work with an overseas prototype manufacturer, understand the local laws and regulations regarding IP protection. Enforcement may be more difficult than in your home country.
For most products, a combination of patents, NDAs, and strategic partnerships built on trust is an effective way to protect your IP during the prototyping phase. With some forethought, you can safeguard your design while still advancing the development process. Of course, be sure to seek legal counsel before proceeding to assess and mitigate risks.
Design for Manufacturability (DFM)
As you develop your prototype, consider how the design will translate to large-scale production. The practice of optimizing a product design for ease of manufacturing and assembly is called design for manufacturability (DFM). Considering DFM principles early in the prototyping process can save significant time, money, and headaches down the road.
Some key DFM considerations for prototype manufacturing include:
- Material selection: Choose materials that are readily available, easy to process, and compatible with your chosen manufacturing methods. Avoid specialty materials unless absolutely necessary.
- Tolerances: Specify reasonable tolerances based on your manufacturing processes’ capabilities and your design’s functional requirements. Tighter tolerances generally increase cost and lead time.
- Feature sizes: Design features like holes, slots, and wall thicknesses to fall within the capabilities of your chosen manufacturing process. Consult with your manufacturing partner for recommended values.
- Draft angles: Incorporate appropriate draft angles on vertical walls to facilitate ejection from molds and dies. This is especially important for injection molding and casting processes.
- Undercuts: Avoid undercuts and other complex geometries that require expensive tooling or secondary operations. If unavoidable, consider breaking the design into multiple parts that can be assembled later.
- Part consolidation: Look for opportunities to combine multiple parts into a single component to reduce assembly time and cost. This is one of the key benefits of additive manufacturing processes like 3D printing.
- Fastening and joining: Use standard fasteners and joining methods wherever possible to simplify assembly and reduce inventory costs. Avoid expensive custom hardware unless absolutely necessary.
Designing for production upfront will help streamline the transition from prototype to production. Work closely with your manufacturing partners to identify potential issues and optimize your designs for manufacturability.
Choosing the Right Prototyping Company
Prototyping with an experienced manufacturing partner allows teams without extensive in-house resources to transform their ideas into physical products for demonstration, testing, and early market validation. But how do you find a prototyping company to trust with your idea?
- Experience: Look for a partner with a proven track record of successful prototype development and a deep understanding of your industry and product requirements. For example, if you’re creating a new medical device, choose a company with experience in biotech.
- Expertise: Ask about their capabilities, equipment, and materials to ensure they can meet your specific needs. Experienced prototyping companies will also likely have valuable input on your product design and point out any potential issues early on.
- Delivery times: Creating a new product prototype often takes weeks or months and multiple iterations to get it right. Ask the company about their typical timelines for different types of projects so you can determine if they align with your goals.
- Cost: Prototyping is an investment, but prices can vary significantly between companies. Get quotes from multiple firms to determine a fair price for your specific needs.
Whether you’re an inventor, a startup founder, or even a large company with limited product development resources, the right prototyping company can help you turn your concept into a tangible reality. By selecting the right prototyping company, you can ensure your prototype puts you on the path to a successful product launch.
Ready to get started with prototype manufacturing? Contact StudioRed today to discuss your project and receive a custom quote. Our team of experienced prototyping experts is dedicated to helping organizations of all sizes bring their innovative ideas to life.