Being an engineer at an accomplished product development company means a constant back and forth to achieve a new product’s function and the “look” of the product. This requires constant back and fourth between the industrial design team and the mechanical engineering team. The look or design of the product will be its face on the world, and how customers meet and interact with the device. It may even communicate the character of a new company, the brand, but it still has to deliver on working well, and meet cost and delivery schedules.
Most products are developed in parallel these days with different disciplines coordinating but also progressing toward production at the same time. So when is it worth making engineering change detailed development for the updated industrial designed look of the product? This could cost a company thousands if not hundreds of thousands of dollars, and worse it could delay time to market and the ability to meet key introduction deadlines. The answer is: When the change will increase sales. Some will say it is all about a homogeneous design vision being realized, and that sounds great, but if you are late to market, 15 percent over budget and it makes no difference in how the product is received by the market, then why do it?
We see this come up when we are helping client’s push to a new product introduction and the industrial design presents an unanticipated look and opportunity that was not foreseeable, and the client loves it. This is often a great thing to have happen, but if the new look that captures the imagination of the client and development team, which, by the way, means it will most likely do the same for the market, is a concept that means major engineering changes or challenges, then the product’s road to market just became a high mountain pass. The team needs to carefully assess if it is really worth it versus just running ahead. A classic example is the 2015 Ford Mustang.
Automobiles have been called the ultimate personal, mobile product. The redesigned for 2015 Ford Mustang has been a tremendous success, and this is no small feat for a legacy product. Talk with an automotive designer and they will eventually admit that iconic automobile lines (think Mustang, Camaro, Corvette, Porsche 911, VW Bug, Jeep CJ) aren’t quite the dream project to work on as they might seem as there is a linage that needs to be honored and slews of diehard fans that have strong expectations of what a new version should look like. Not as much fun for a designer as a clean sheet of paper design. How then to keep it fresh but tied to the past.
Ford arguably achieved this and with the help of some very talented individuals. Ford also had marketing reasons to be ready for the 50th anniversary to show off the new car model and cut off market share gobbling competitors, so the schedule did not allow for slip room. Additionally, specialty cars don’t sell in the same numbers as F150’s and Toyota Camary’s so budgets are a bit sensitive. However, during the 2014 introduction of the 2015 Mustang the team shared how important maintaining the developed new look had been to them. It seems that during creation of the body, the fenders grew at the rear to wider haunches late in the process, and this updated look was well liked by the team, but with the engineered chassis and components developed for the new 4 wheel independent suspension having been designed for the earlier, narrower rear body work, there was going to be a problem in bring the newer wider look together. Would changing the rear suspensions track width and components be worth it or could the car go to market with a weird looking inset at the rear or should Ford just scrap the cooler looking rear body panels?
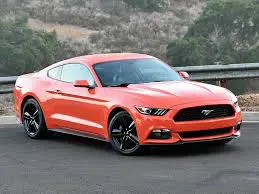
Given past negative reviews of poorly fitted wheel and tire packages to the Mustang bodies of the ‘80’s and ‘90’s which left odd gaps to comply with corporate ground clearance requirements the idea of just fitting the newly engineered but narrow rear end to the wider 2015 body was not a good idea, but the updated wide design look was viewed as a winner, so Ford spent the money and squeezed in the time to re-work the rear suspension design. Now if you have ever approached the end of a new and complicated design with a myriad of important interacting details, on schedule, and you now hear about a change to the look of the outer body that will require revisiting a lot of the engineering work just finished, and – oh, by the way – you can’t change the end date of the delivery schedule, it is enough to drive you crazy. However, the Ford team, and a multitude of new Mustang owners, all seem to agree it was worth changing the engineered parts to take advantage of the improved, if not late in the schedule, wider look of the Mustang, and the share of the market captured would seem to confirm that. The narrower body would not have been as striking and mis-fitted inset wheels would have not had the finished look needed to run in the current specialty segment of the automotive market. The change resulted in a better product and the market reacted.
An alternate example also comes from the automotive world as well. This time it is about 1990 and the Mitsubishi derivative, the Dodge Stealth, is a surprise on the automotive scene. It shows up with much technology, and from a design stand point it has many surfaces and contours and plastic panels. As a young engineer I had wondered about those plastic vent like bumps on the hood above the head lights and in front of the windshield. How much engineering went into serving their important function, were they originally intended to be scoops, or … It turns out that they were located above the shock absorber mounts, and back in those early days of 3D solid CAD modeling and parallel development the sleek look of the car’s body had been decided on but the shock mounts had been forgotten about. The solution in this case was not to work out a change to the look (raising the hood would have had a negative over all affect) or re-engineer the front suspension (although to be fair there may not have been too much of an option there), so the fix was kind of a bandage. Add a plastic “power bulge” cover to the hood of the car on each side to cover up the holes cut in the hood to clear the shock towers, and make the plastic add on look cool, sort of.
Today it would be difficult to find a development team willing to fix this mistake this way, and the look of the Dodge version of the car, in particular, was never praised to the level of many of its contemporaries. At a time when plastic add on’s were still OK, it sufficed, but I think it is valid to wonder if more Dodges would have sold if the look had been cleaner, and apparently Mitsubishi and Dodge agreed as a more contoured hood without attached covers appeared before the Dodge version left the market in ’96. The more integrated solution was better and would have been worth the effort, especially when placing these vehicles in comparison to the offerings emerging in the segment from Mazda, Nissan, Toyota and Porsche.
So what about other product categories? We had a client that had developed a much improved simple western method of analyzing proteins in an automated system. They already offered a line of products that worked, but these had a complicated, dated look. The improved next generation product was a working mock-up on a table in the lab and they had developed a new app interface for users. A simpler working experience was the relationship that they wanted to draw customers to. Their improved technology and product, and the look and interaction had to convey that relationship.
When projects like this start out none of the experienced management or engineers at the client or product development consultancy say, “Hey, let’s make some of the parts of the this project as difficult to produce as possible, and we should plan on just spending extra money to get there.” However, as the robotic internals where being co-developed for this light tight product that required user access and clearances to the outer skins for a door and mechanisms to be laid in, the industrial design team here proposed a look that was a knock out, and in more ways than one because although it captured the simplified language desired and told the story of a better way to work in this category, the product’s outer body would have fully orthogonal sides with very tight part to part fits that had to be co-planner. Most plastic parts and housings have draft in them. Think “sides of a cup cake” coming out of a pan. They are tapered so the finished goods can slide out, but if the outsides of the plastic housing are all at right angles to each other, and the top and the bottom, then the plastic part will not slide out, so the metal tool that the plastic is molded in needs to have moving walls called side actions. Additionally, the inside of the plastic housing parts are hollow and these surfaces need drafted walls too (think middle of the bunt cake) or very complex moving parts in the core metal of the molding tool to release the plastic part from the mold.
Quite simply the look was worth it though and engineering would have to take on the challenge of not compromising the look while meeting a reasonable cost target. Don’t get me wrong, the engineering department suggested a little bit of draft on the outside walls, pointed to iconic forms like pyramids, and explained how the staff would prefer to be able to go home on time, but fully right angled outside housing walls and doors were developed, and even more challenging was the inner features to meet up with a light tight frame that required developing lifter mechanisms and moving components in the metal core of the tooling. Post injection molding, cooling fixtures were devised to ensure these very large plastic housing parts did not have their flat walls warp or sag which would take away from any hope of the surfaces being co-planner. Everything had to line up, and the plastic housing was to be finished in shinny paint, so any imperfection would catch a highlight and spoil the intended effect.No draft on sides, minimal gaps and no off sets to hide misalignments between panels – tough challenge / great look!
The first plastic housings were photographed and marketing material was released. Production parts were on order to build the first units for sale, and all projected sales figures were blown away. The units sold per month went up 3 fold. It was a combination of the ease of work flow and the look conveying that new simplicity. If the product had only looked like a mild evolution of the older, bulkier units, it would not have hit the market like it did, and help the client claim a market segment for them self. The engineering changes and challenges to work with the look that told the message was clearly worth it. It led to a brand language and repeat business for all involved.
So next time you think you have the internal mechanisms engineered and ready for a new product ahead of schedule just remember there may be an industrial design parallel development that will be definitive in the market, and it is best to re-work the guts to make the best of it to truly be epic, as long as it will sell more. To speak with a product development company expert, contact us.