Draft is that necessity in injection molded part design of angling surfaces on the sides of the part so that it can come out of the mold. These surfaces of the injection molded part might have been intended to be parallel and not pyramided in, but then the part might stick in the metal molding tool or at least scrape the newly formed plastic side faces as it is removed.
In fact draft is a key aspect for the product design of injection molded parts as it can play havoc with the intended product’s look, form and fit up in the assembly if not properly considered early on. Designers and mechanical engineers of plastic injection molded parts have to take into consideration the design intent, part alignment and ease of manufacturing.
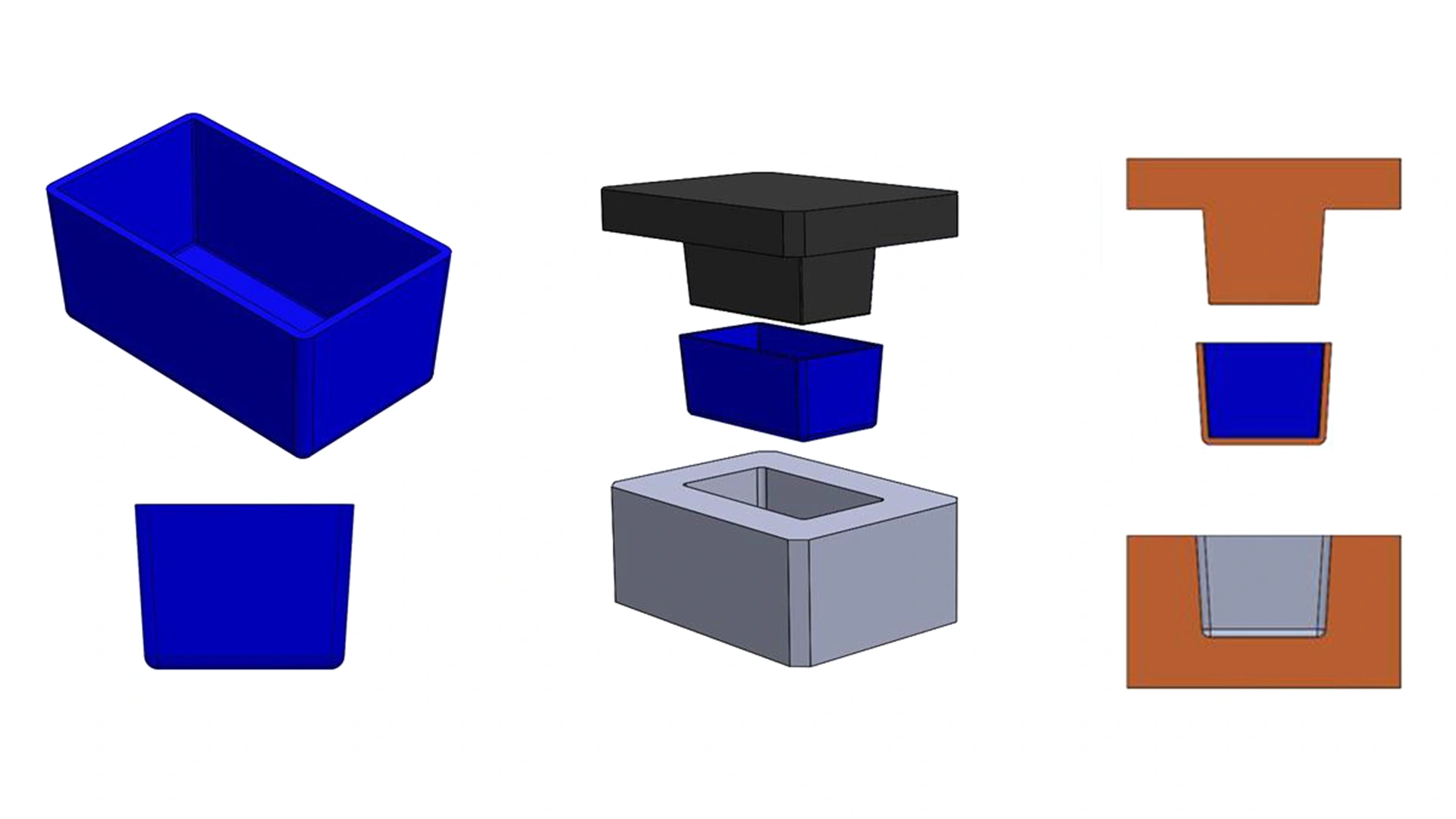
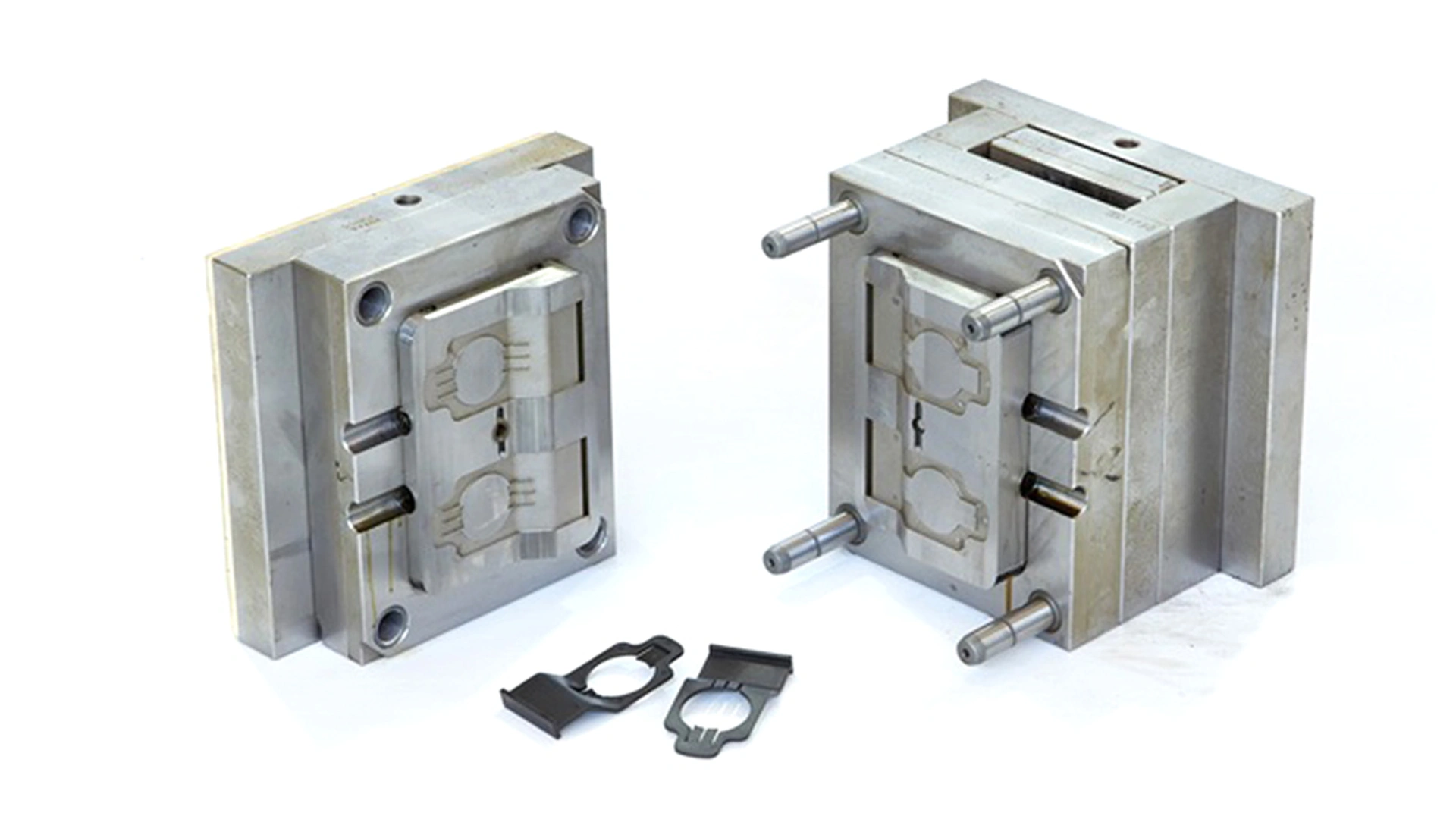
The injection molded plastic parts being designed will have to be formed in a large metal cavity created in the two metal halves of the mold where molten plastic is to be pushed into under pressure. When the plastic cools and solidifies the main tool halves separate and eject the new part. The more draft on the side walls of the plastic part the easier it is to get the part out of the mold, and the faster.
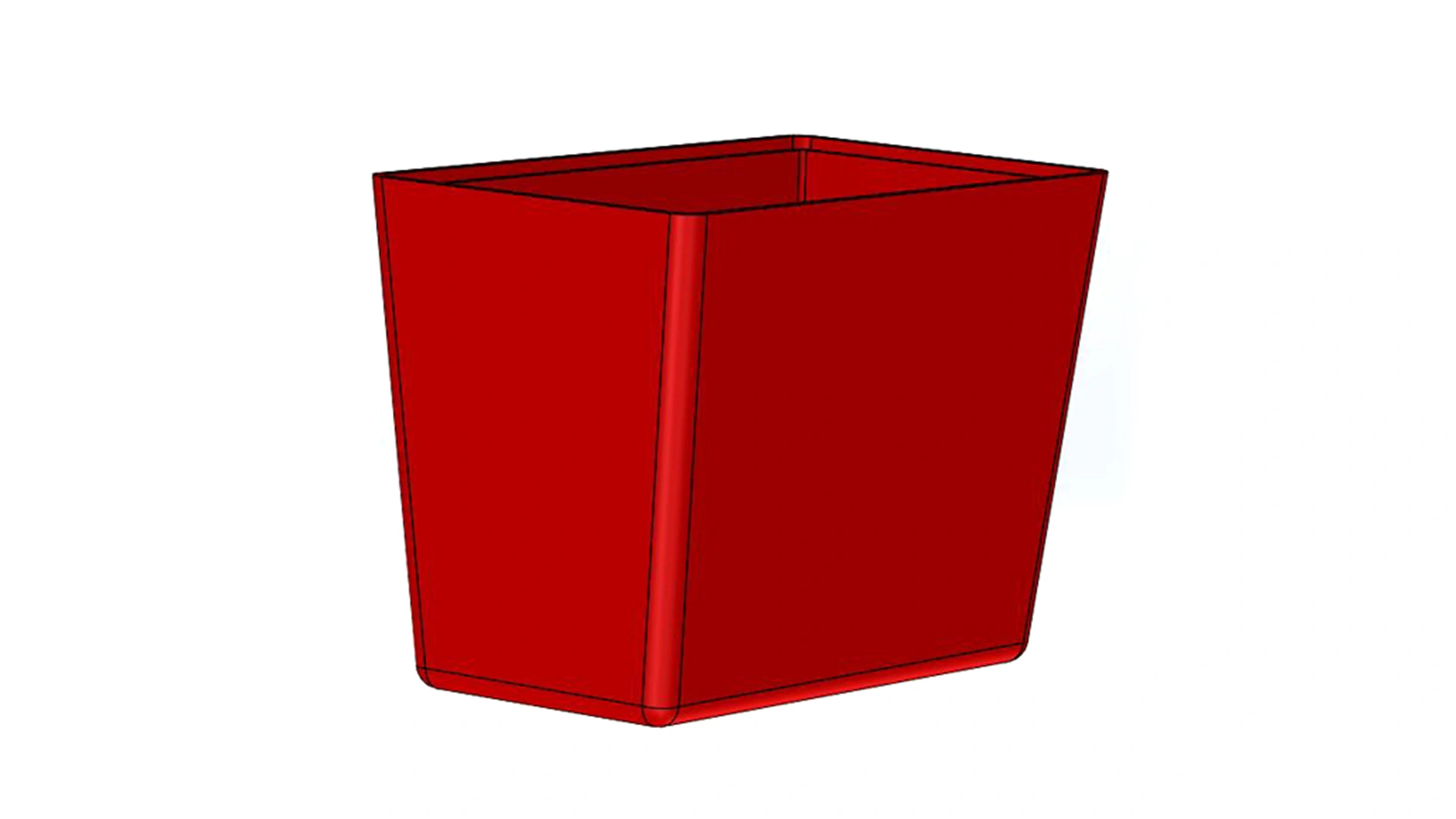
If an injection molded plastic part has a heavy texture or pattern on the molded side surfaces, the pattern will actually be made up of very small high and low spots. An inset low spot in the injection molded plastic part would require the metal mold tool to have raised material that might catch or drag on the newly formed plastic part’s sides if they were not drafted enough.
Image via grabcad.com
Finish sample sheet shows mold texture options, etched in to the metal mold using various methods. The more contoured the finish, as noted in the finish depth, the more minimum draft called for to ensures newly formed textured plastic sides do not scrape on the metal tool during ejection from the mold.
Usually, additional draft is needed as the texture relief deepens. A good general rule and what previously had been recommended by Mold-Tech was 1.0 to 1.5 degrees of draft for every 0.001 inch of depth of texture, but recommendations for this are often higher draft angles for interior walls as plastic injection molded parts shrink as they cool and therefore increase drag on these mold surfaces.
Also, some molders will recommend more draft to basically make their job easier and lower risk issues with the finish on parts, less risk of parts sticking in molds, and increased injection cycle times which sometimes just means increased profit margin for the molder.
So this makes it seem like more draft would always be better, and if all our product designs went to a point that could be the case. Often for clearance to internal components, or a tight fitting compact design, or a simplified and rectilinear look that calls for plastic parts that have parallel walls, draft is in opposition. This can increase tooling cost and risk with maintaining injection molded plastic part finishes.
So how far can we push back on draft? There are compromises that can be reached. The needed draft is driven by several factors including material, cycle time, de-molding concerns, and finish, which we have been talking about. The goal is actually to try to have the best outcome for all concerned, but this may mean some compromise is needed in some areas.
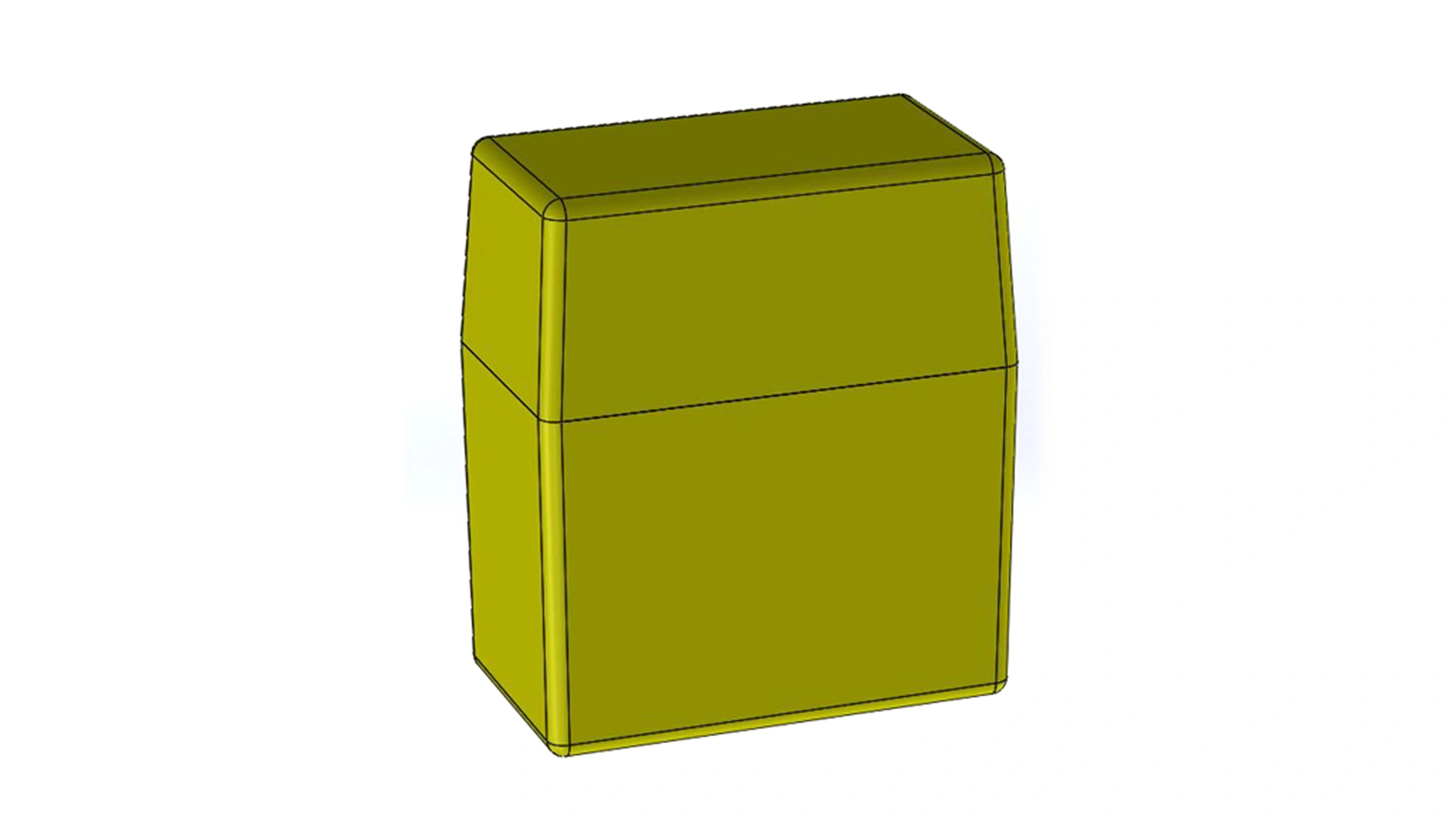
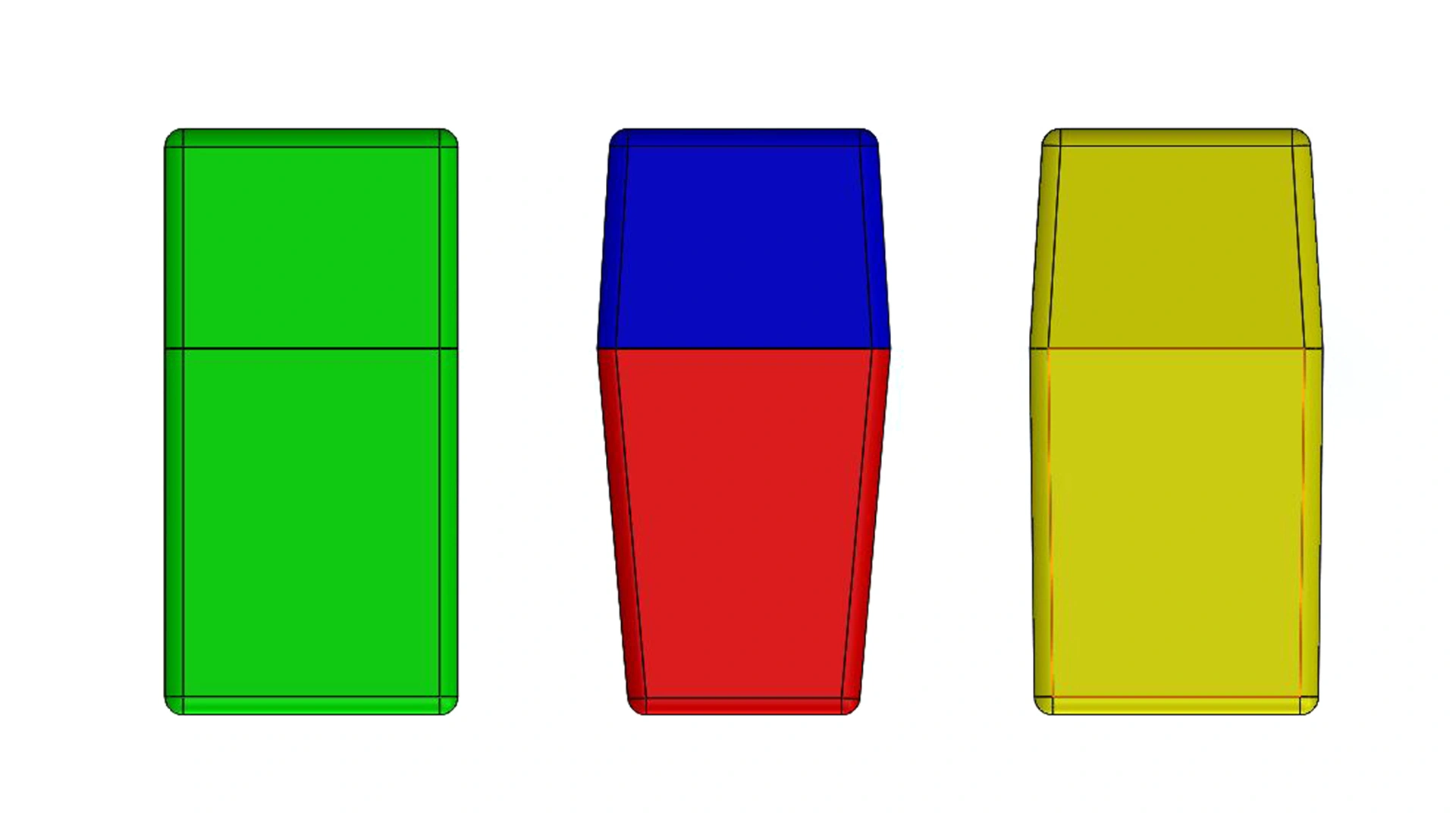
It is not uncommon to work with the industrial design team, client and molder to reach the best outcome. Perhaps texture is lightened some to relieve a bit of the draft needed. A step smoother on finish is often not that perceptible. The interior surfaces, if smooth, can have lesser draft too so as not to thin out the walls and interior ribs to much at the top of taller parts.
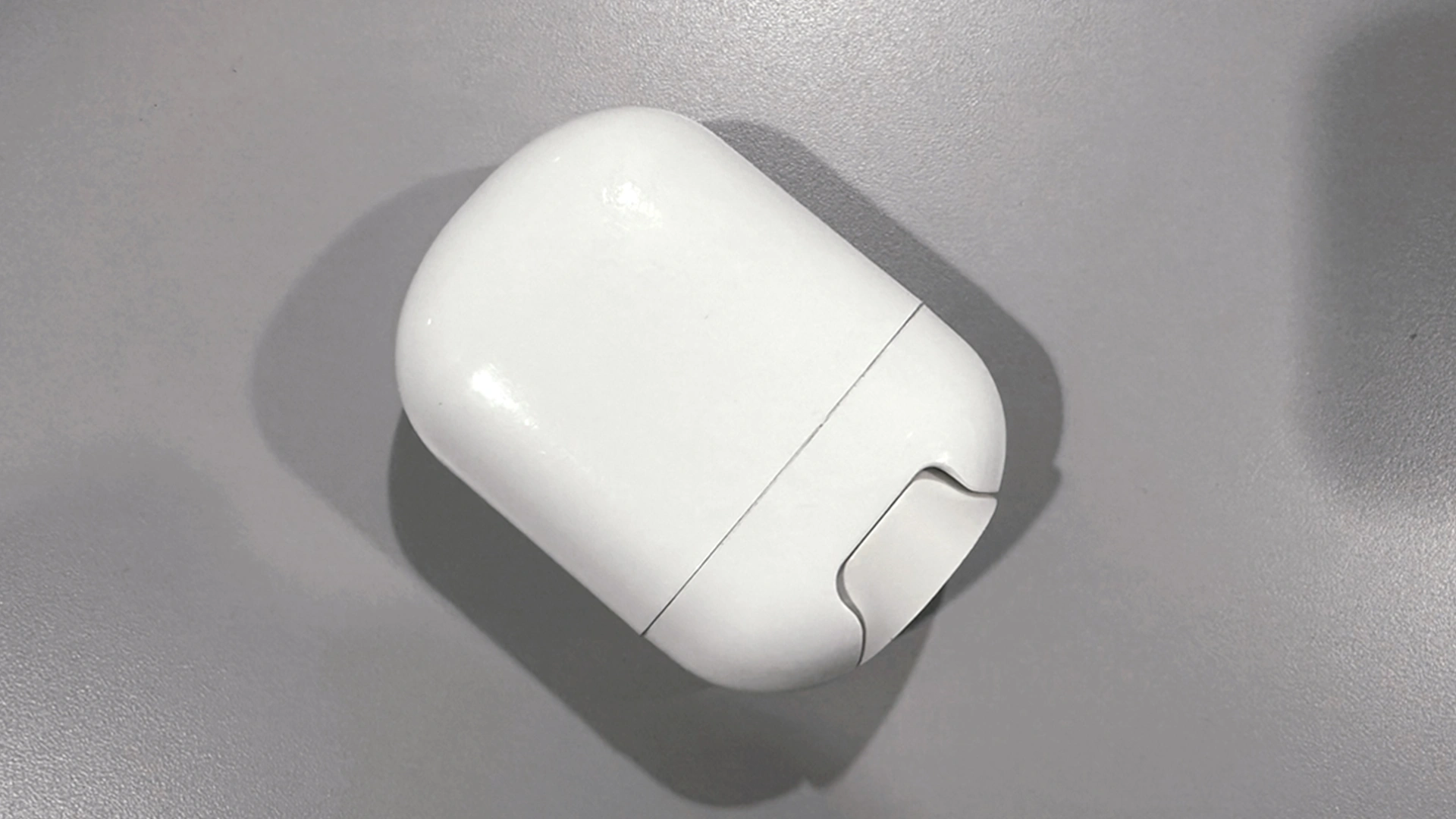
The leeway in the draft for texture recommendations on outside surfaces can permit working with the molder and their process. They may have less concern with certain materials and lower volume parts as cycle time is less crucial and more cooling time means the plastic part will pull away its outside surface from the metal tooling mold around it. Texture can also be “faded” out if curved surfaces near tangency at part lines for alignment of mating parts, and equate to near zero draft angles in those regions for example.
As a product design consultancy we too often see products and plastic parts that were designed in a sketch at one point and then left to a contract tooler overseas to interpret and mold, as cheaply as possible, and the client comes to us wanting us to fix the poor outcome after they have spent hundreds of thousands of dollars.
Product design of injection molded parts is a team effort, and the whole team should be included in the process and decision making throughout the project to get the best results. This integrated approach, including engineering for injection molded part design, also saves money and time to market. So now you have an angle on injection molded plastic part draft.
See More Like This: Undercuts, Sink Marks, Bosses